Why MMAD Testing Matters in Inhalation Product Development
The benefits of working with a full-service consultancy
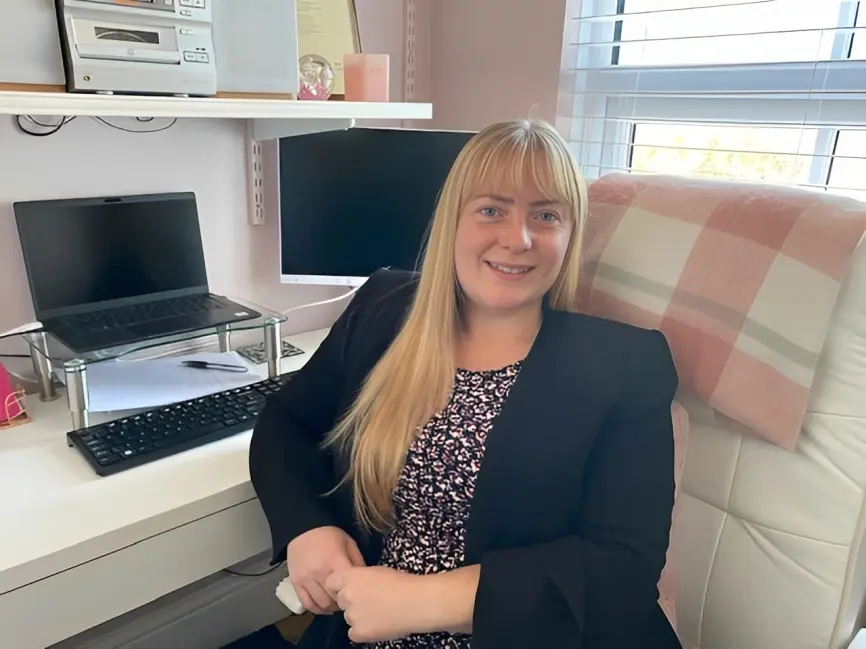
Apr 14, 2023 | Published by Nicola Selvey
To bring a pharmaceutical product or Electronic Nicotine Delivery System (ENDS) to market, a business needs expertise in product development and assessment, analytical testing, toxicology, stability and quality control, to name but a few. It also needs knowledge of the regulatory environment, where change can be particularly fast-paced in emerging markets. Many firms choose to outsource parts of their process, such as extractables and leachables (E&L) testing, but what is the best approach when looking for a service provider? Here Nicola Selvey, PMO Manager at Broughton, explains how a full-service consultancy can help bring life-enhancing products to market more efficiently and cost effectively.
It has now become common practice in our industry to offer each area as a siloed service when outsourced, rather than as part of a full service. An information silo is defined as a system or team that is unable to freely communicate and share information with other systems and teams. In simple terms, it means that when a firm has expertise in highly technical areas, it might not be sharing knowledge effectively between them.
Information silos are common in all industries — data from McKinsey & Company shows only one quarter of senior executives report that their teams effectively share knowledge across the organization — but are particularly troublesome when trying to achieve market authorization for a drug product or designing a new medical device. For example, you might work with a consultancy team when developing your product, but then send it elsewhere to test it for regulatory compliance, with limited communication between the stages. How a drug product is designed, from API and formulation to its packaging and shelf-life, will determine what testing strategy needs to be applied — if these services are siloed then the interdependencies might be missed, which can have a significant impact on the cost and timelines of a project.
It’s easy to see how life science organizations can become siloed, however — teams may have fragmented workflows in highly specialized areas, which can act as a barrier to sharing critical knowledge between groups. This, in turn, can lead to costly decisions being made based on inadequate or outdated information. As science becomes more interdisciplinary, which research shows it is, consultancy firms must recognise this by facilitating collaboration between teams and recognising they’re all part of the same process. At Broughton, that’s exactly what we aim to do.
Building a strategic partnership
At Broughton, we prefer to develop a strategic partnership with our clients, offering scientific solutions to their problems rather than individual services. For example, we have product design consultants, who work closely alongside E&L experts and toxicologists. This allows our team to recognise the interdependencies of, let’s say, the chemistry of a formulation and the toxicology tests that must be carried out as a result. Or, if a certain material is used in the packaging, we can recognise how it might degrade and leach into the formulation after being stored for an extended period of time. Knowing how each part of the process is related allows us to plan the optimum number of tests, in the minimum amount of time, to create a robust data profile of a product.
A large part of this is in how a project is managed. At Broughton, each project is given a dedicated Technical Project Lead (TPL), whose task it is to ensure strategic planning and technical oversight, tying up all the loose ends and making sure a cohesive scientific strategy is in place. Our project managers are then on hand to oversee delivery and consistent communication with the client. This end-to-end style of project management — rather than having a project passed around between different team members — helps ensure that none of the important details are missed.
Once these considerations have been made, the testing strategy can be implemented, and we do this in-house too. For example, our on-site storage and analytical testing facilities help minimize lead times, since products don’t need to be transported elsewhere in the midst of a stability test. Once a product is on the market, we can use our understanding of how it was developed, alongside our quality control batch release testing capability, to ensure it complies with the highest of standards.
Visit our website to find out how Broughton’s full-service analytical testing and scientific consultancy can help develop your nicotine, cannabinoid and pharmaceutical products: https://www.broughton-group.com/